Inventory Management
Best-in-class inventory management with our electronic shelf label solution
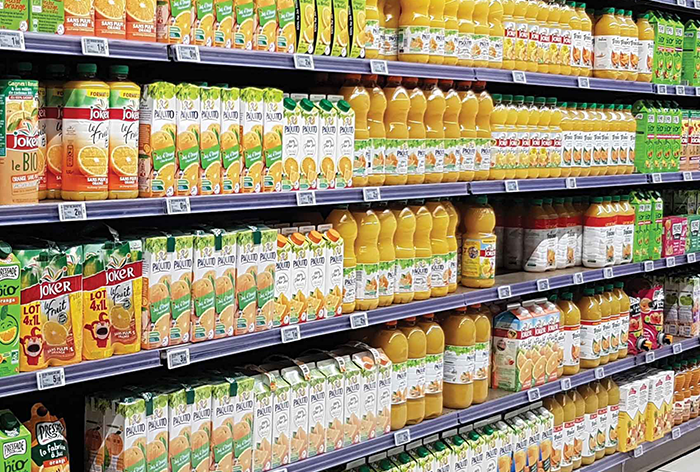
The Challenge
Most retailers today use automatic ordering to supply their stores. For many reasons, the process is not optimal and it is common to have inaccurate stock levels. Consequently, many stores either have too little or too much inventory of a given product. Too little means lost sales, while too much means tied up capital as well as the risk of never selling all of the stock.
The Solution
Many strategies are used to keep stock levels as accurate as possible, and the Pricer system can help too. The first method is to simplify the search for suspect stock levels by highlighting products with a low or even negative theoretical stock. This can be done before the store opens by flashing all labels that are associated products with low stock levels or by doing targeted checks throughout the day, guided by Instant Flash and a map showing where the products to check are.
Other methods are more indirect, although still very effective. By using the flash-guided solution, replenishment errors are drastically reduced in the first place. For example, the guided replenishment avoids the common mistake that a product is put in front of a very similar looking but not identical product, thus hiding the one behind and invariably leading to mistakes further on.
Simplify your store’s inventory management
Running out of stock, or having the wrong stock level, are major concerns for today’s retail. Improve your stores’ stock data and simplify inventory checks with Pricer inventory management.
Modern retail supply chains are typically built on automatic ordering where orders will be placed on stock levels and sell-through rates. Unfortunately, stock level data is notoriously hard to keep accurate.
There are many different root causes for this such as products in the wrong place, broken multi-packs, multi-rebates, waste, theft and inaccurate supply data. In order to fix the data regular shelf inventory checks are continuously done, another time consuming and error-prone task. All the locations for the products must be found and the units counted. Again, finding products is not easy.
The solutions
Pricer offers two slightly different solutions that simplify inventory management.
Solution – checking before the store opens
The first method is to simplify the search for suspect stock levels by highlighting products with a low or even negative theoretical stock. This can be done before the store opens by flashing all labels that are associated with products that have low stock levels or by doing targeted checks throughout the day, guided by Instant Flash and a map showing the location of the products to check.
The first method is carried out outside opening hours by shifting all labels to a staff page that shows supply chain-related information such as stock level, next delivery date, batch sizes and similar. This is usually coupled with flashing the labels where there is reason to suspect that the data is bad or that something is wrong, typically negative theoretical stock and non-moving items.
Negative stock means that the theoretical stock in the system is less than zero, which is obviously not possible; non-moving items are when the system sees that an item which normally sells fast have not sold any recently (can be during the day or for a full day depending on the POS-data available). Inventory checks are thus greatly simplified by using flash to bring immediate focus. Flashing can also be used for high priority items (items on promotion, with high margin or seasonal).
Solution – checking during the day
The second solution is to find critical items throughout the day. The employees again use Instant Flash and map to locate the items to check. The same checks can of course be made here: negative stock, non-moving items or high priority checks.
The value of the solutions is both on time save and in improved stock level data. The latter is very important for e-commerce and for not binding up more capital in stock than absolutely needed.
Other solutions
Other methods are more indirect, although still very effective. By using the flash-guided solution, replenishment errors are drastically reduced in the first place.
For example, the guided replenishment avoids the common mistake that a product is put in front of a very similar-looking but not identical product, thus hiding the one behind and invariably leading to mistakes further on in the replenishment chain.
Customer experience
Pricer’s solutions for inventory management are widely used by our customers. One example is a major retail chain with 650 stores, ranging from convenience stores to supermarkets and hypermarkets, in a European country that has used these solutions for several years allowing employees to work more easily and efficiently.
Every morning, until 15 minutes before the store opens, they shift the information on the labels to display the inventory status which is also shown on their personal digital assistant (PDA). They can check the theoretical stock, last day of order and ordered amount, planned or past delivery dates and quantities, the average sale of the week, etc. directly on the shelves and for each of the products.
Thanks to the interconnection of the Pricer ESL system with the customer’s own back-office applications, their reference prices are shown on the labels, but the Pricer system can collect the information concerning the management of the stores and display them on the additional pages on all labels whether they are segment or e-paper labels.
The speed of the Pricer communication system based on infrared technology allows the system to be set so that these management pages are displayed at a time set by the store. It is also possible to view these pages in real-time using Pricer’s remote control, a simple but flexible tool for various kinds of shelf edge use cases.
Prerequisites
To ensure scalability and reliability of a solution like this there are several pre-requisites.
Firstly, the system must be able to operate in real-time. The labels need to be capable of immediately showing up to date information and to change within a minimal time (e.g. one second) to ensure that no time is wasted during the checking period.
Secondly, the system must be fully integrated with the store management back end applications to allow fully integrated data to be displayed directly next to every product on every shelf.
Specific prerequisites
- Solution 1 – switching pages in the morning
– Long flash time, which is supported by all Pricer labels.
– Possibility to do two display updates every day, on top of everything else. This is supported by all Pricer labels.
- Solution 2 – checking products throughout the day
– Instant Flash (every second waiting for the flash is a second not saved).
– Dynamic Product Positioning (to generate up-to-date maps for the staff to find the products).
Enter your email below to download a PDF version of the page
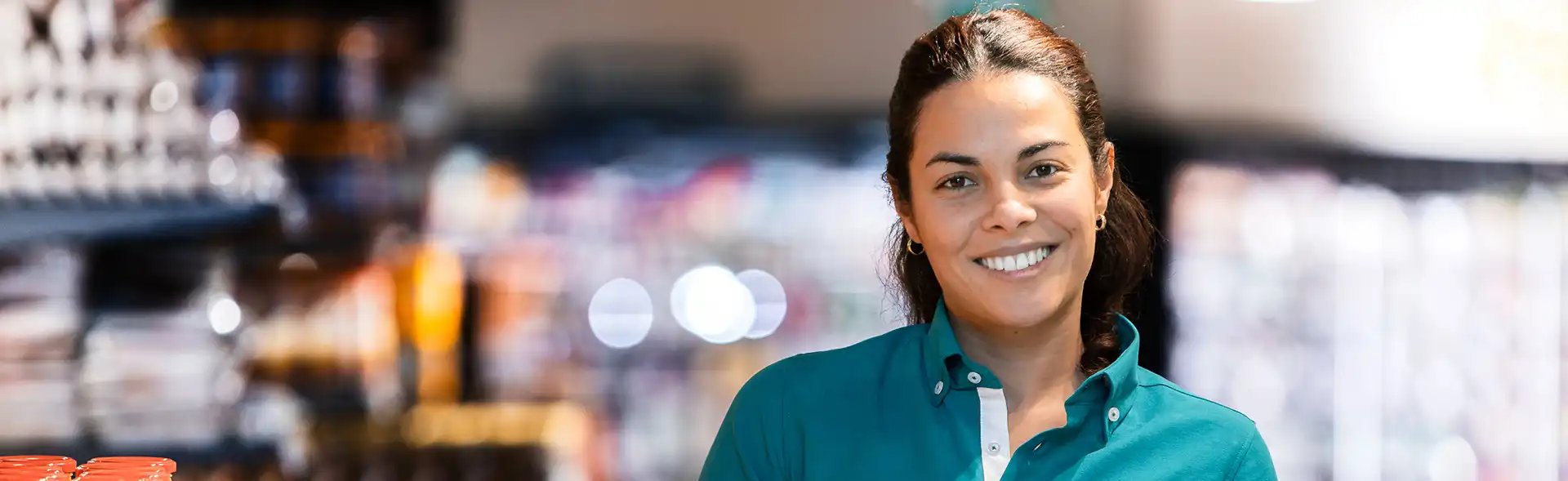